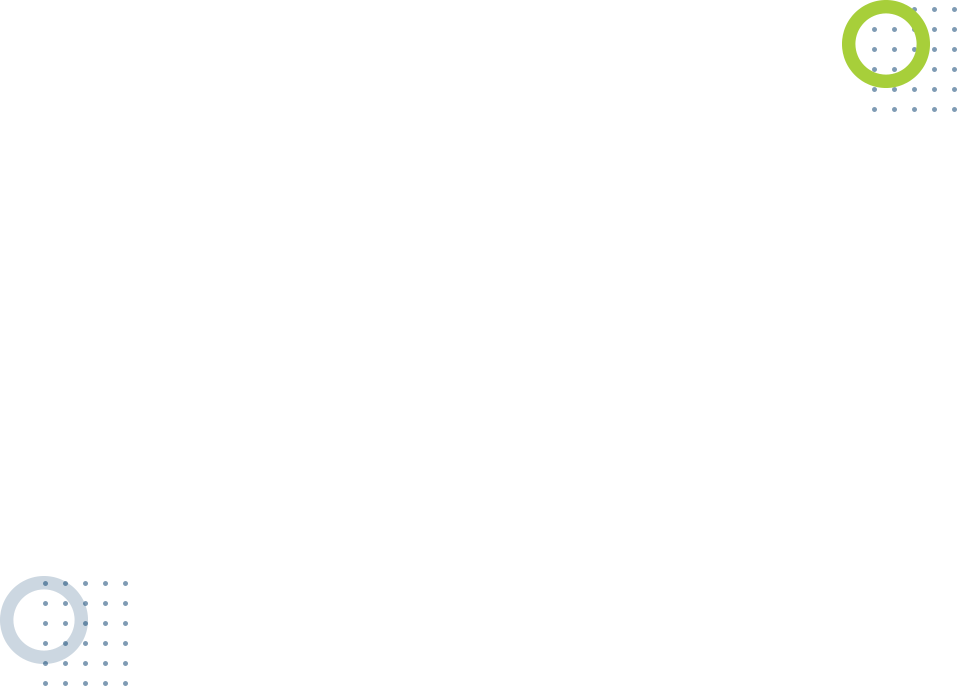
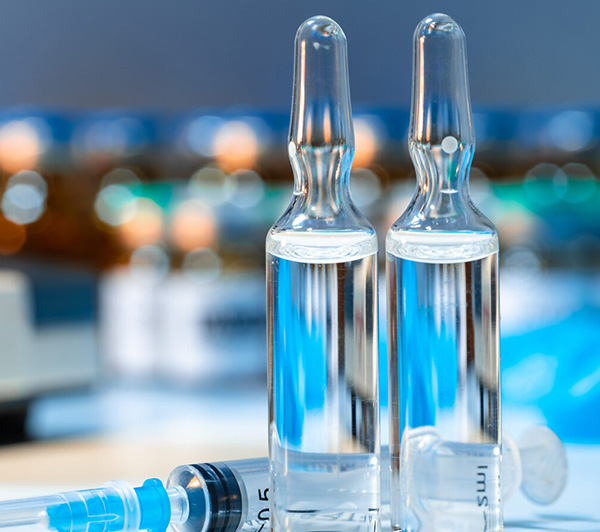
GMP CERTIFICATION
GOOD MANUFACTURING PRACTICES
GMP refers to the Good Manufacturing Practice Regulations promulgated by the US Food & Drug Administration under the authority of the Federal Food, Drug, & Cosmetic Act for ensuring that products are consistently produced and controlled according to quality standards. The Good Manufacturing Practice Regulations GMP was finalized in April of 1969 and published as Part 128 of the Code of Federal Regulations (CFR). In 1977, Part 128 was recodified and published as Part 110 of the CFR. The Good Manufacturing Practice Regulations are divided into five sections: General Provisions (Subpart A) on personnel, which delineates plant and employee responsibilities with regard to personal hygiene, Subpart B of the food GMPs outlines requirements for the maintenance, layout, and operations of food processing facilities, Subpart C describes the requirements and expectations for the design, construction, and maintenance of equipment and utensils so as to ensure sanitary conditions, Subpart E - Production and Process Controls that include general sanitation processes and controls necessary to ensure that food is suitable for human consumption and Subpart G - Defect Action Levels - for some natural or unavoidable defects. These regulations, which have the force of Law, require the Manufacturers, Processors & Packagers of Drugs, Medical Devices, Food, and Blood to take proactive steps to ensure that their Products are Safe, Pure, and Effective through a Quality Approach that enables the companies to minimize or eliminate instances of Contamination, Mix-ups, & Errors. Good Manufacturing Practice Regulations cover all aspects of production from the starting raw materials, premises, and equipment to the training and personal hygiene of staff. Thus, detailed written procedures aligned with the manufacturing process are also important since they can impact the final product's quality. There must be systems to prove that consistent procedures are followed at every stage of the manufacturing process.
Principles
Principles of GMP Certification
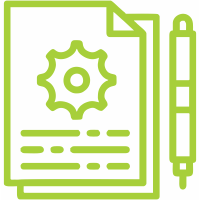
Define & Create
SOPs & Work
Instructions

Enforce & Follow
SOPs & Work
Instructions
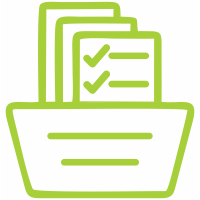
QMS Documentation
& Record
Keeping

Quality Management
System &
Process Validation

Define & Design
Equipment &
Construction Facilities

Maintenance
of Facilities &
Equipment

Defining, Developing
& Demonstrating
Job Competence

Protection
Against
Contamination

Quality
Assurance
& Management

Controlling
Components &
Product-Related Processes

Complaint
Redressal &
Management
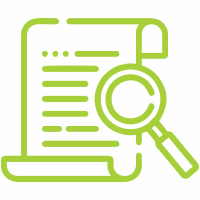
Conduct Planned
Inspections & Periodic
Quality Audits
benefits
Benefits of GMP Certification
Consumers ultimately receive products that are high quality, safe, and suitable for consumption.
GMP provides a clear production guideline ensuring that products meet the expected quality standards.
Ensures reduction in the number of errors or deviations that result in non-standard products.
Ensures Compliance with Business, Legal, Contractual, Statutory and Regulatory Requirements.
Helps establish a simple and standardized system for tracking data and information.
Promotes a healthy control system with highest cleanliness and sanitation standards.
Provides Suppliers with greater confidence thereby building Mutually Beneficial Relationship.
Provides International Reputation & Recognition, Branding, Credibility and Competitive Advantage.
Better Hazard and Risk Detection and Management with Increased Supply Chain Control.
Provides New marketing opportunity and strengthen the trust of Customers and Business Partners.
Potential increase in Business due to enhanced Customer Confidence and Satisfaction.
Increases the Company’s Business Revenue, Profitability and ROI by Reducing Costs.
service portfolio
Our Services Related to GMP Certification

PRE-AUDIT GAP ASSESSMENT SERVICES
Available across all Management Systems and Standards, Pre-Audits Gap Assessments allow you to Assess your Management System's Readiness and Save your Time and Money that would otherwise be spent on Redundant Audits. A Pre-Assessment Audit is performed with the same independence and objectivity as a Certification Audit.
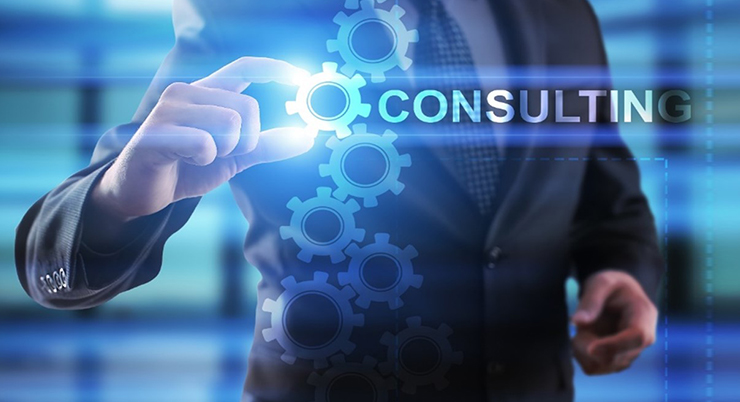
ADVISORY & CONSULTANCY SERVICES
Quantum Systems has established a reputation for "Building User Friendly, Efficient and Sustainable Management Systems that incorporate Industry Best Practices and that comply with the highest International Standards. Quantum System's provides a 'One-Stop-Shop' for all Social & Technical Management System Consultancy needs.
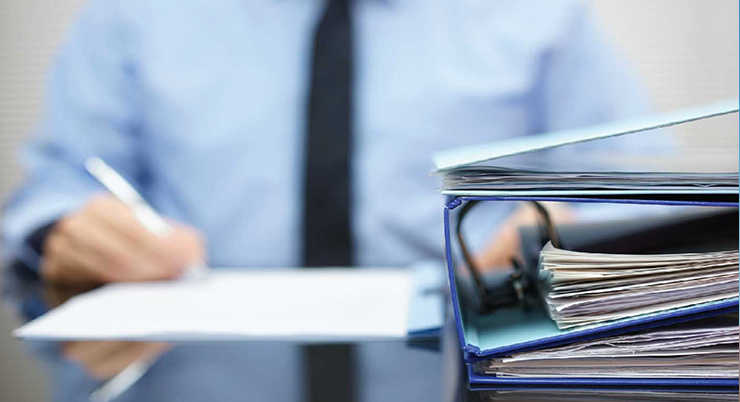
ACM SERVICES
We can help by designing a Cost-Effective Annual Compliance Maintenance (ACM) Program to suit your Company’s Individual Needs and Expectations. The ACM Services Contract Proposal is based on Parameters like Facility Size, Production Capacity, Workforce Strength, Number of Production Sites and Standards covered in the ACM Contract.
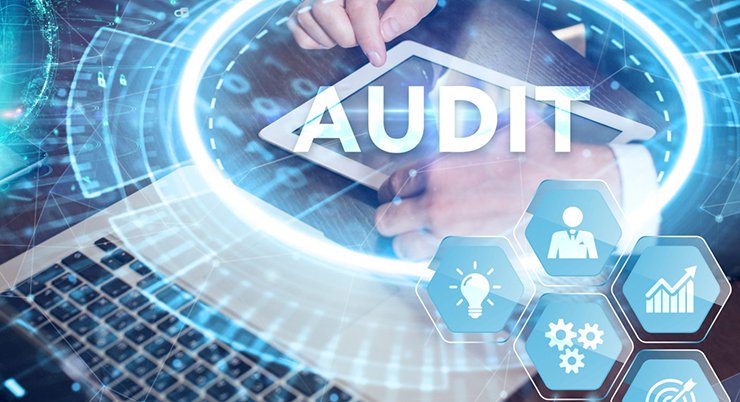
BUYERS COC AUDITS
We provide Advisory Services on Buyers COC Audits for Global Brands like Walmart, Sears, Next, Marks & Spencers, Macy’s, Kohl’s, Levis, Esprit, JC Penny, Adidas, Nike, Carrefour, Li & Fung, Coles, Amazon, ALDI, LIDL, El Corte, Kaufland, ASOS, Bata, Armani, Muller-Meyer, Costco, Nautica, Timberland, Clarks, Inditex, Woolsworth, Clarks, Bunzl, Debenhams, Superdry etc.
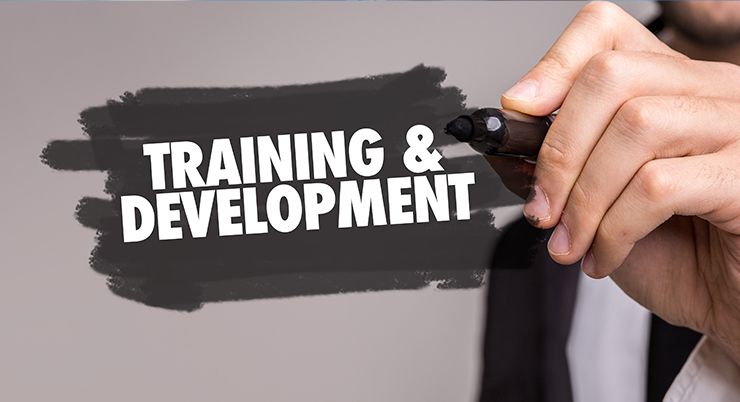
TRAINING & CAPACITY BUILDING SERVICES
Our Training Courses cover International and Regional Regulatory Developments, Good Manufacturing Practices, Social & Technical Management Systems Certification, Evolving Technology & Markets etc. We impart trainings on a wide spectrum of courses through different modes like Classroom Trainings, Virtual Trainings, Webinars and eLearning.
@2021 Quantum Systems Management Private Limited ©